Maglev 200™ System
High-fidelity interaction with virtual or remote environments
The Maglev 200™ Magnetic Levitation Haptic Interface incorporates several important advantages which are listed below.
Six degrees of freedom
Most haptic devices have only 3 degrees of freedom, allowing virtual objects to be positioned in space while reflecting forces back to the user. With six DOFs, both the position and orientation of a complex 3D virtual object can be manipulated while experiencing forces and torques. (The Maglev 200™ has six DOFs and can be upgraded to add a 7th user-supplied DOF that can be used, e.g., for grasping.)
Single moving part
The single moving part ("flotor," analogous to a motor's rotor) of the Maglev 200™ acts much like a simple inertia floating in space, without the resonant peaking typical of linkage-based devices.
Zero static friction
Static friction is the enemy of precision motion. The Maglev 200™ does not have any static friction, but does have a small amount of physical damping, strictly proportional to the speed of the flotor, which aids in control. Additional damping or even stick-slip friction can be easily simulated through software.
Zero mechanical backlash
Mechanical backlash or lost motion introduces unwanted hysteresis. The Maglev 200™ is free of these effects.
High bandwidths
The Maglev 200™ has very high position bandwidths, enabling high-fidelity rendering of subtle friction and texture effects. High force bandwidths are achieved by using high slew rate low-noise linear amplifiers, very low coil inductances, and rigidly connecting the handle to the flotor. (The flotor can move with up to 8 g's of acceleration.)
High position resolution
An important feature of the Maglev 200™ is its very high position resolution, near the limits of human perception. The high resolution, in part, makes it possible to operate effectively within a small, comfortable workspace.
Wide stiffness range
As a consequence of its simple rigid body control model and high resolution, the Maglev 200™ is capable of rendering a range of stiffnesses from essentially imperceptible to extremely hard. At the highest stiffnesses, it is difficult to distinguish between contacting virtual surfaces and contacting real surfaces.
Interchangeable handles
One handle does not serve all needs. The Maglev 200™ has a simple molded handle resembling a small mouse with a pair of buttons. This basic handle can be interchanged with other handles. Supplied documentation allows custom handles to be designed and interfaced to the Maglev 200™. (See the section on "Interchangeable handles," below.)
Mechanical simplicity
For many years our philosophy has been to trade mechanical complexity for computational complexity. The Maglev 200™ exemplifies this approach, where there are no tight tolerances and operation is completely sensor-based. In terms of mechanics, it would be hard to get any simpler.
Comfortable operation
Haptic devices are not traditionally known for their comfort of use. However, the pose of the Maglev 200™ is adjustable in its tabletop mounting to suit the user (see table data sheet). Operation at an angle allows the forearm to be at a comfortable attitude with the wrist resting lightly on the device housing. The motion range of the Maglev 200™ is approximately matched to the comfortable range of fingertip motion.
Interchangeable handles
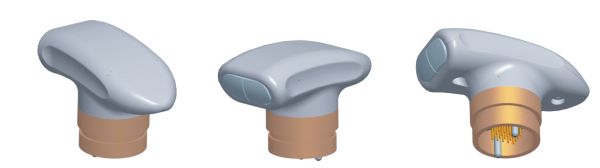
Shown above is the 2-button mouse-like handle supplied with the Maglev 200™ system. Additional types such as pen-like and joystick-like handles will be available. The handle-flotor interface specifications are supplied to enable the development of customized handles for particular applications. In particular, the system supports the addition of a 7th DOF by providing a current output which can drive a small actuator as well as providing a ratiometic analog input. These functions are supported by the API and Graphical Monitor Program. Please refer to the handle connector data sheet for more information.
More detailed information on the Maglev 200™ system
Design features
Degrees of freedom | 6, upgradable to 7 |
---|---|
Amplifiers | Low noise linear |
Handle | Interchangeable |
Included handle | Mouse-like |
Handle buttons | 2 |
Device pose | Adjustable 0-90 deg. |
Device mass (Model 201) | 18 Kg |
Device diameter | 0.40 m sphere |
Controller mass (Model 202) | 14.5 Kg |
Controller dimensions | 0.20 x 0.45 x 0.53 m |
Power requirements | 115V/6A, 230V/3A |
Performance characteristics
Translational workspace | 24 mm dia. sphere |
---|---|
Rotational range | +/-8 deg (see note 1) |
Position resolution (1 sigma) | <2.0 microns |
Angular resolution (1 sigma) | 3.6 arcsec |
Position bandwidth (-3dB) | 140 Hz |
Force bandwidth at handle | >2000 Hz |
Peak force (Z axis) | 40 N |
Force resolution | 20 mN |
Peak torque (Z axis) | 3.6 Nm |
Maximum translational stiffness | 50 N/mm |
Minimum translational stiffness | 0.002 N/mm |
Maximum rotational stiffness | 5.1 Nm/deg |
Minimum rotational stiffness | 0.01 Nm/deg |
Backdrive static friction | 0.0 N |
Mechanical backlash | 0.0 microns |
Perceived mass (flotor) | 616 g |
Maximum servo rate | 4000 Hz |
Levitation power | 4.5 W |
Stray field at handle | 0.001T |
Software
Embedded RT operating system | QNX™ 6.3 |
---|---|
Communication | 100 Mb/s Ethernet |
User interface (C/C++ language) | Structured API |
Testing and debugging facility | Graphical monitor |
Host OS compatibility | Linux, Windows |
Haptic API Compatibility | CHAI 3D, MATLAB® |
Note 1: Rotational range is reduced near the limits of the translational workspace.
Candidate advanced applications
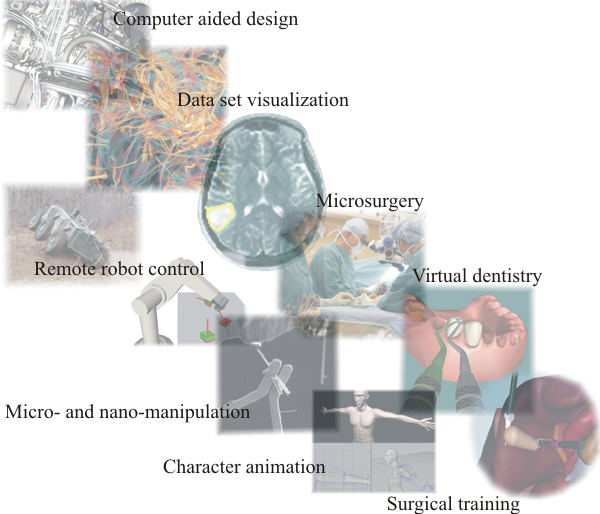
There are many interesting and important research issues concerning haptic interaction. Maglev haptic technology has been used for the psychophysical investigation of human touch with virtual environments simulating hard contact, textured surfaces, and deformable objects. Additionally, it has been used in teleoperation of a robot arm and control of a mobile robot. The Maglev 200™ can be thought of as a precision instrument or tool suitable for a wide range of scientific pursuits. Besides research use, we look forward to seeing the Maglev 200™ employed in the investigation of a number of advanced applications. What is your application?
Ordering your Maglev 200™ system
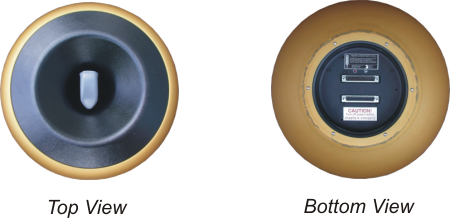
Model 201 Device.
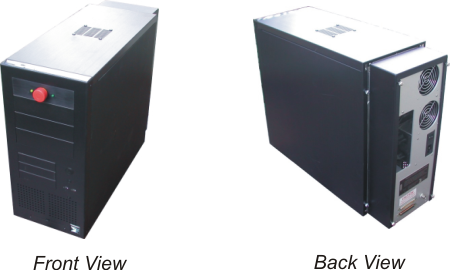
Model 202 Controller.
The Maglev 200™ system includes the Model 201 device, Model 202 controller, cables, detachable mouse-like handle, desktop mounting kit, manuals, and client-side software (API, graphical monitor, and demos). Information is available in a printable system data sheet. Optional modular tables for configuring visual-haptic workstations can be ordered. Please see the table data sheet. Owners of Maglev 200™ systems automatically enjoy benefits of the Magnetic Levitation Haptic Consortium.